You’re not alone if you think the news cycle has been a bit much to handle lately. Among all the shocking headlines vying for our attention, there’s been a recurring theme:
The Broken Global Supply Chain.
It seems like we have been talking about supply chain issues for a loooong time now. Wait, we have! The problems were expected to work themselves out by now, but many shelves remain bare. Lingering COVID lockdowns in the manufacturing centers of China pose another unpredictable risk.
“This has caused uncertainty for Chinese factories and manufacturing plants, which have had to suspend production and introduce “closed loop” systems, with workers remaining on site. The ratings agency Fitch says the restrictions have also caused significant backlogs at the port of Shanghai, the world’s largest container port, adding to existing supply chain disruptions. With around 15 per cent of global merchandise exports originating in China, the agency warned that shortages of manufactured goods could worsen and that this would contribute to global inflationary pressures.” –newstatesman.com
If offshore manufacturing to gets back up to speed, will the ports be able to handle the load?
Current indicators point to further congestion at the ports for the time being. California’s gig-work law, AB5, is further complicating domestic trucking capacity at our western ports. Cargo had already been routinely snarled in a logistics bottleneck once it arrived at a U.S. port. Carriers will often not hesitate to slap fees on shippers in order to get the empty container back. From 2020 to 2021, the average demurrage and detention charge increased by a whopping +104%. To further complicate matters, the historically high price of fuel shows no sign of normalcy for now. Volatile oil markets add upward pressure to the cost of international shipping. The current cost for a single 40’ container to make the trip across the pacific stands at more than ten thousand U.S. dollars.
As the price of bunker fuel continues to rise, shipping companies will undoubtedly resort to slow steaming which adds additional travel time. Good luck to companies that still rely on the just-in-time manufacturing model of years past.
Foreign manufacture presents a unique risk.
We haven’t even talked about the inherent risk to intellectual property yet! It’s no secret- theft of American IP is a huge issue. The U.S. Customs and Border Patrol maintains a dashboard to tally seizures of counterfeit goods and the numbers speak for themselves. Keep in mind that this data only accounts for counterfeit goods that were shipped back to the U.S. instead of heading to international markets. The total annual losses are undoubtedly much higher.
When taken in concert, these factors indicate that cheap foreign manufacturing just isn’t worth the risk anymore. Domestic manufacture is looking more and more like the way to go. But where do you start? It can seem daunting to make the leap to “Made in the U.S.A.” Now for the good news- it can be done! We’ve helped clients successfully reshore their operations with reverse engineering and short-run manufacturing support. To make the process as smooth as possible, Catalyst has compiled the top seven keys to reshoring your manufacturing operations.
When you keep these 7 key aspects in mind, reshoring your product’s manufacturing will quickly result in long term benefits.
A reduced global footprint provides a more reliable production schedule with faster shipping times. Enjoy clarity and speed in communication with your manufacturing partner without vast differences in time zones and holidays.
Made in the USA carries value for your customers by demonstrating your commitment to employing more people domestically. If your customer had a choice between similar products, would they pick the U.S. made option?
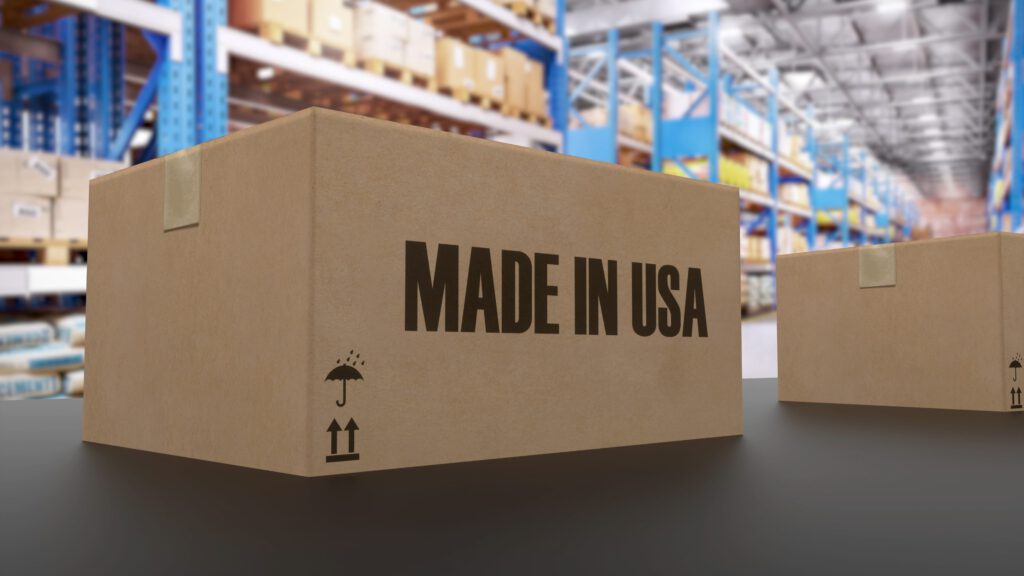