The Additive Advantage
3D printing is at the forefront of today’s fast-paced world of product development for good reason. Additive manufacturing offers a quick and economic leap forward in the complex journey from a simple, unproven idea to a tangible, market-ready product. 3D printed prototypes have been proven to be an important aspect of the overall picture. A general understanding of the capabilities and limitations of 3D printed prototypes helps to bring their role in the overall process into sharper focus.
Catalyst is in a constant state of innovation to rapidly create new products that cater to the ever-evolving demands of consumers. Our rapid product development process is a comprehensive, six-stage approach that takes a new product from its conceptual stage to a fully realized, market-ready item. Over the past 25 years, this process has been proven time and again as an efficient and effective way to bring a new product to market.
The Six Stages
Research | Design | Engineer | Prototype | Tooling | Manufacture
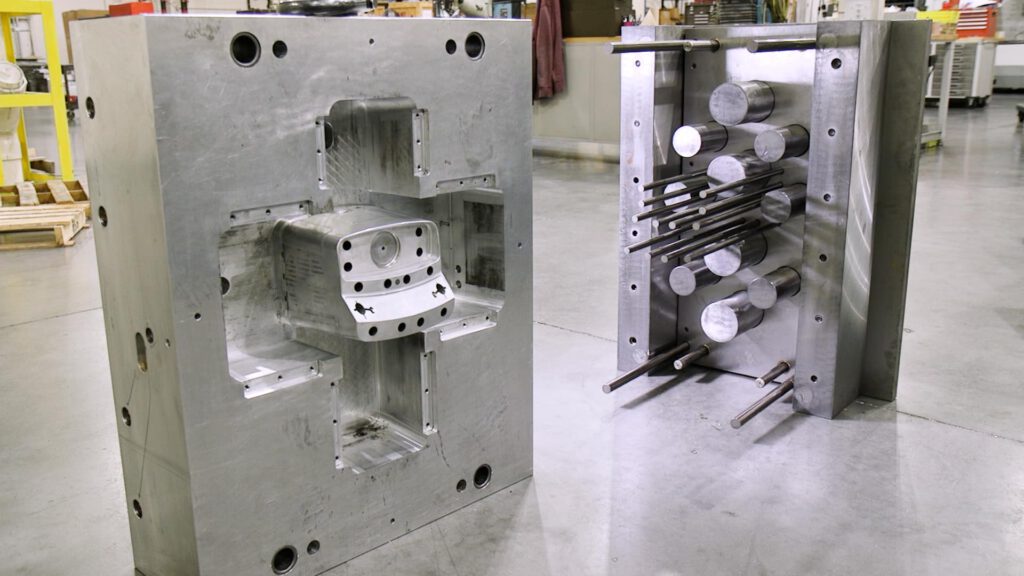
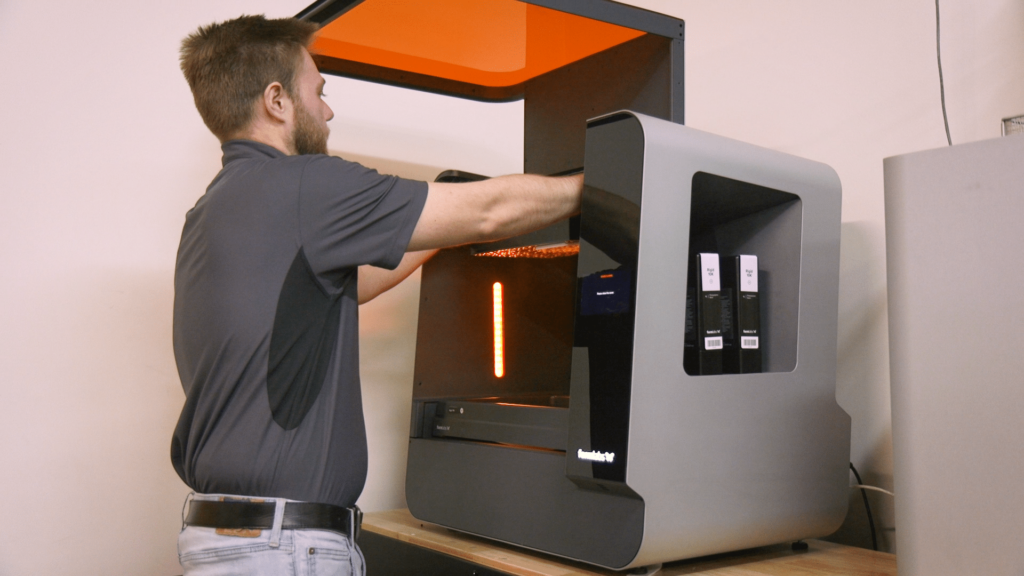
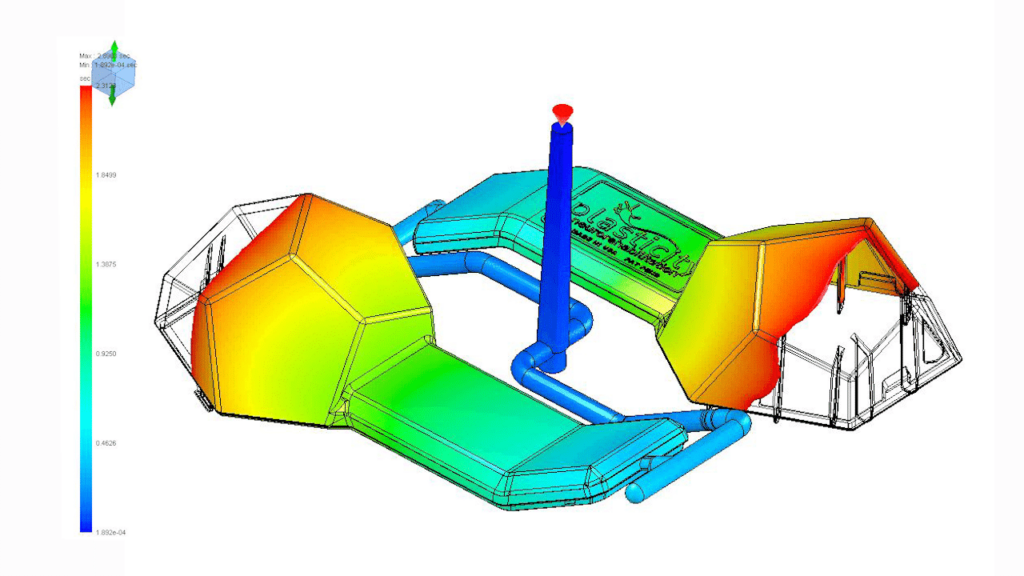
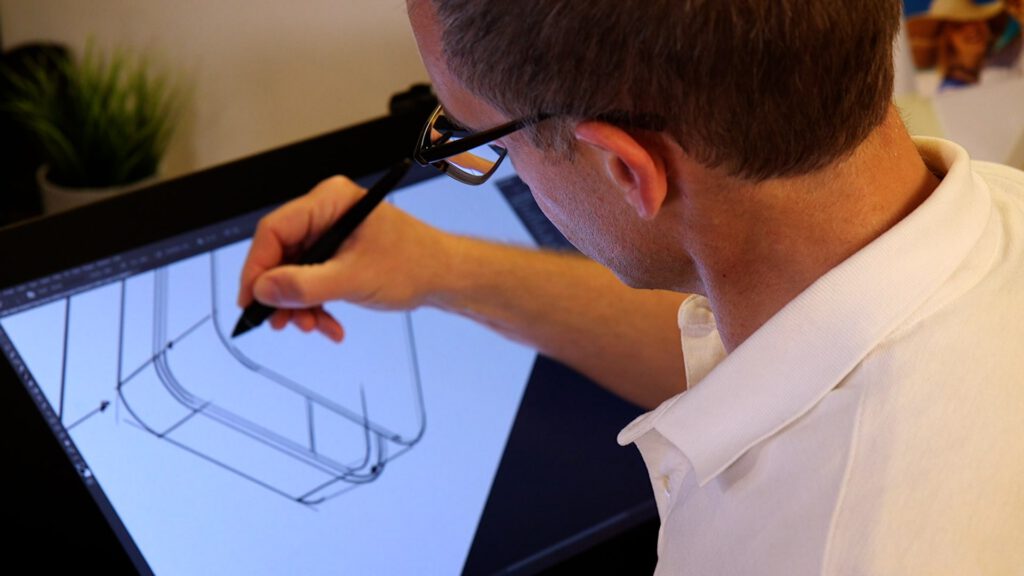
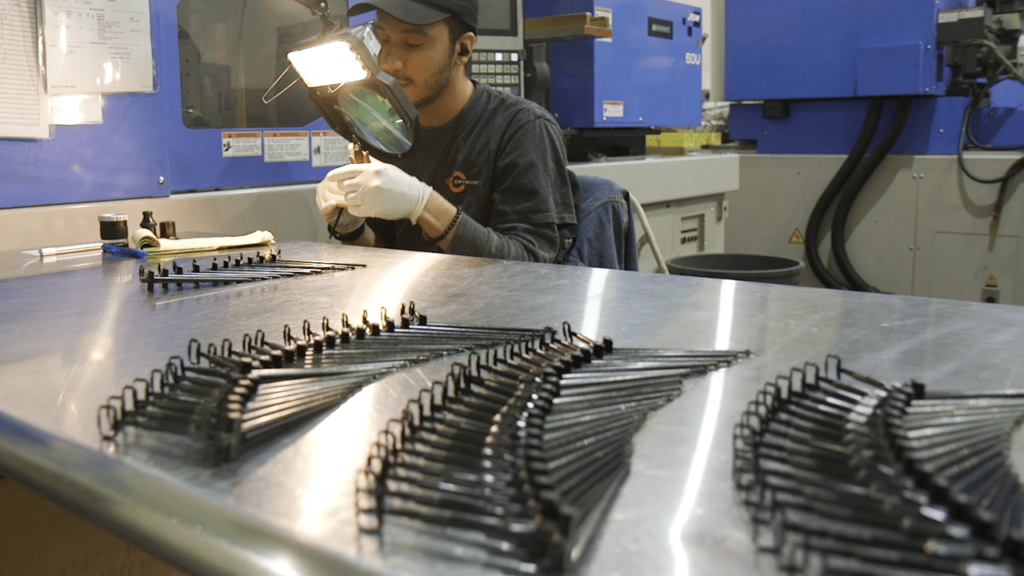
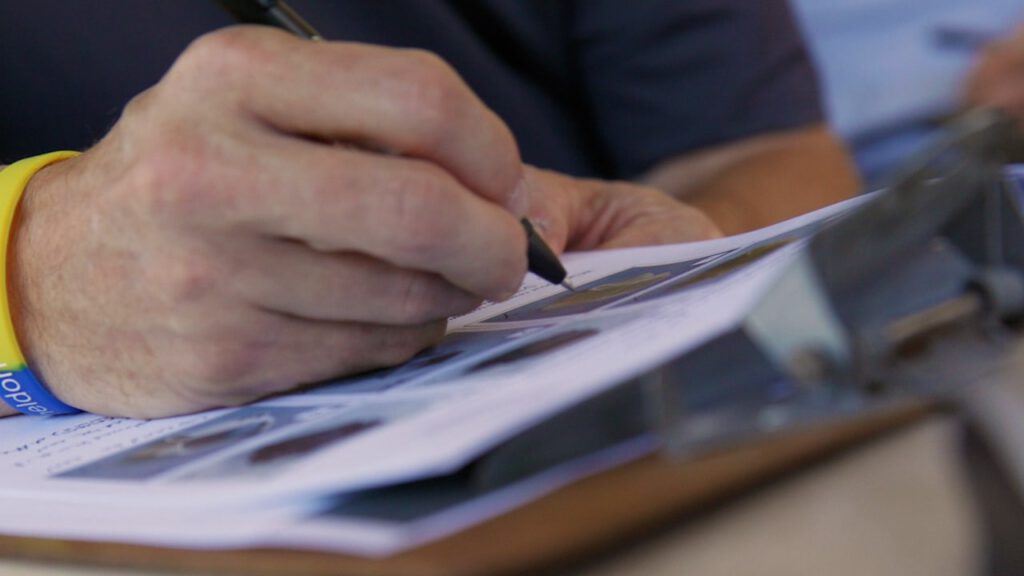
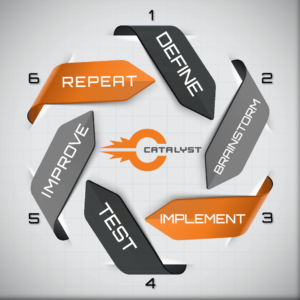
A crucial aspect of the process is to remain flexible and adaptable while navigating unexpected hurdles that arise along the way. This is where the concept of a circular path within the process comes into play. At any point, a project may require revisiting a previous stage to define an issue, brainstorm solutions, implement an action plan, test the new outcome, make further improvements based on new data, and repeat as necessary. Quick decisions and rapid iteration is essential for ensuring the ultimate success of the project.
Rapid Iteration
Among the stages of Catalyst’s product development process, the prototyping phase often stands out as particularly exciting and highly anticipated. The creation of a physical prototype opens the door to extensive real-world testing, which is vital for fine-tuning the product. Yet, as exciting as the prototyping phase is, it can also reveal undesirable traits or flaws. This might necessitate iterative work within the design and engineering phases to address these issues effectively. Therefore, it’s crucial that a prototype is both quick and cost-effective to produce while still serving its intended purpose as a testbed for the product’s viability and functionality. We recognize the importance of offering a range of prototyping methods to cater to the unique needs of each project. Clay modeling, room-temperature-vulcanizing silicone (RTV), urethane castings, and CNC modeling allows us to tailor the prototyping process to each project’s specific requirements. However, 3D printing is often regarded as the most versatile and cost-effective method for creating prototypes and functional parts.
One of the most common questions we receive from clients is about the types of 3D printing we offer and the characteristics of each method. It’s a crucial consideration because the choice of materials and printing methods can significantly impact the properties and characteristics of the final prototype. The following sections provide a brief comparison of different materials and methods commonly used for 3D printing prototypes at Catalyst. This will help you make informed decisions about the best approach for your unique project, ensuring that your prototype serves its intended purpose effectively. So, let’s delve into the 3D printing services available at Catalyst and discover how it can bring your innovative ideas to life.
Catalyst 3D Printing
Plastics (Fused Deposition Modeling – FDM):
• Materials: PLA, ABS, PETG, TPU, and more.
• Strength: Typically moderate, with variations depending on the specific plastic used.
• Applications: Basic prototyping, concept modeling, functional parts, consumer goods.
Method (FDM):
• Process: Extrudes thermoplastic filament layer by layer. Maximum build volume of 300 x 300 x 605 mm (11.8 x 11.8 x 23.8 in)
• Pros: Affordable, wide range of materials, double head extrusion to incorporate multiple materials in a single component, available direct drive at the extruder heads for more reliable outcomes.
• Cons: Limited surface finish, layer lines visible. Requires more post-processing to achieve a finished appearance.
Resins (Stereolithography – SLA and Digital Light Processing – DLP):
• Materials: Photopolymer resins (e.g., standard, flexible, tough, high temperature, translucent).
• Strength: Can vary widely, with some resins approaching the properties of engineering plastics.
• Applications: High-detail prototypes, medical models, intricate parts.
Method (SLA):
• Process: Uses a UV laser to solidify liquid photopolymer resin layer by layer.
• Pros: High detail, smooth surface finish, diverse resin options, less finishing work required for presentation level appearance.
• Cons: Limited to smaller build volumes of 335 x 200 x 300 mm (13.2 x 7.9 x 11.8 in), post-processing cleaning and curing required.
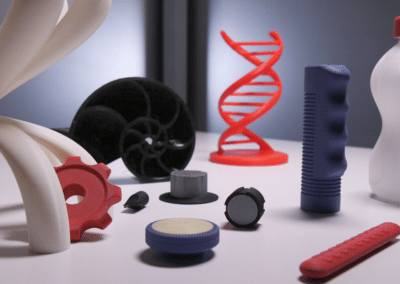
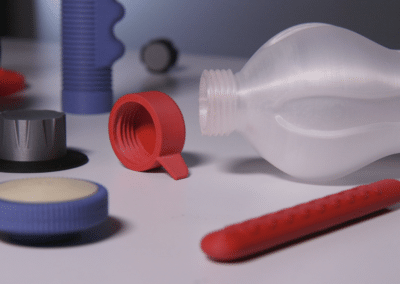
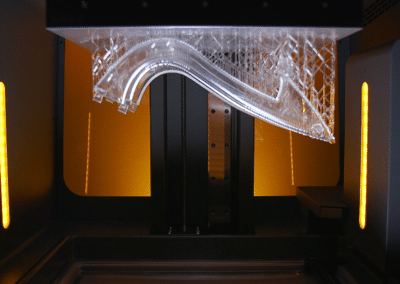
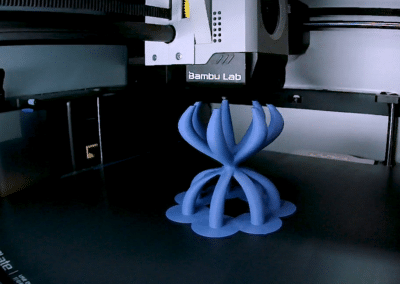
Decision Time
The choice of materials and methods in 3D printing plays a pivotal role in the success of a project. It’s a decision that encompasses various factors, each contributing to the final outcome. At Catalyst, our team of designers and engineers work to ensure that your project benefits from the most suitable combination of materials and methods.
Cost is often a primary concern when embarking on a prototyping journey. Fortunately, 3D printing offers a range of materials that cater to various budget constraints. Whether you’re working with a tight budget or have more flexibility, our experts can guide you in selecting the right materials and methods that align with your financial goals.
The intended use of your prototype can dramatically impact the choice of materials and methods. Some may require flexibility, while others need rigidity. Some may benefit from transparency or translucency, while others demand a specific texture or color. For example, if functional prototype needs to withstand challenging environmental conditions, we’ll recommend materials with the requisite resilience and durability. Conversely, if your goal is to create a visually appealing prototype for a presentation, we can guide you towards materials that offer improved surface finish and detail.
Expert Guidance
Our team understands these nuanced requirements and will work closely with you to select materials and methods that align with the properties required by your project. We don’t offer a cookie-cutter service; we’re about providing tailored solutions to maximize the potential of your product. Catalyst has carefully assembled our fleet of equipment to provide for a wide range of print resolution, material selection, print size and speed. Each machine has a wider range of material options than traditional high-output industry equipment which gives our team more flexibility in testing and problem solving. When it is appropriate to pull in additional resources, Catalyst maintains strategic partnerships around the country to support further options. Selecting the most suitable combination of materials and methods ensures that your prototype is not only an expression of your ideas but also a functional, reliable, and cost-effective tool for testing and refinement.
Whether you’re a seasoned innovator or embarking on your first foray into the world of product development, Catalyst is here to guide you through the intricacies of prototyping. With our expertise, technology, and dedication to your project’s success, we’re ready to transform your ideas into tangible reality. Together, we’ll unlock the full potential of your innovations, bringing them to the market and the hands of consumers.
Need a quick quote? Get in touch with an actual person for a free consultation!