The college experience is typically defined by four years of no parental supervision, long days in class, followed by longer nights out with friends, and finally late morning sleeping in…every early 20-something’s dream. After four years and three summers at home, students leave campus for the last time with a diploma in the mail, and charge into the work force to start their careers.
A four-year college education is vastly considered the norm, but there are some institutions such as The University of Cincinnati, who do things differently. For the few hundred students enrolled in UC’s Industrial Design program in the College of Design, Architecture, Art, and Planning (DAAP), four years turns into five years, and summers off are a distant memory.
DAAP students spend their college years alternating between semesters spent on campus taking courses, and semesters spent on Co-op working anywhere in the country. This means the typical student spends five full semesters working full time, building their resumes, and kick-starting their careers. While the Co-op system can provide endless opportunities for students, none of it would be possible without the support from companies such as Catalyst Product Development Group.
For over a decade now, Catalyst has built a strong working relationship with DAAP by regularly hiring Industrial Design students and providing them with the opportunity to spend their Co-op semester interning for Catalyst. “We feel that students should have opportunities to get real-world work experience as it kickstarts their growth path professionally” states, Creative Services Manager, Paul Zink. “It also allows us to grow new talent from the ground up as we engage students in the Catalyst Product Development cycle from initial concept development through production.”
Catalyst, thanks to its mind to market business structure, has the ability to provide Co-op students with a unique work experience that they are not likely to receive working for other similarly sized firms. In the product development industry, it’s very rare to find a company that has the resources and capabilities to both design products and produce them, all under one roof, but that is exactly what Catalyst does. For the interns, this means that they get the unique opportunity of seeing a project go through every phase of the development process first hand. Their title may read “Industrial Design Intern” in their email signature, but at Catalyst, that doesn’t mean 40 hours a week spent getting coffee, mopping floors, or shuffling paperwork.
Catalyst makes sure that the students are involved with client projects from the very beginning of the process. Students participate heavily in the brainstorming and concept development phase, and then get a front row seat as the project moves on to engineering. Sharing a workspace with the engineering team allows the students to watch their concept develop, and ensure that sacrifices to the design are not made unknowingly. Finally, the engineered concept moves down the hall to the prototyping or manufacturing department, and after a couple weeks of machining and polishing, students can watch as freshly molded parts are ejected from one of the five injection molding presses, in house.
The amount of work and responsibility that Catalyst gives its interns during their time there speaks volumes to the company’s desire to mentor and support the next generation of young designers. Every employee is eager to lend a helping hand where they can, and they all demonstrate a level of great care for the interns’ experience. This sense of duty towards mentorship was especially evident during the spring of this year when Catalyst collaborated with me, former intern Simon Leclerc, to help complete my studio project for my latest semester of coursework in Cincinnati.
I was enrolled in a lighting design studio, where each student was tasked with designing, developing, and prototyping a unique lighting solution for the residential setting. This style of open-ended prompt is quite common for design studio courses in DAAP, because it allows each student to tailor the project towards his or her area of interest. As the semester progressed, Director of Product Development, Andrew Mendenhall, along with Creative Services Manager, Paul Zink showed increasing interest in my lighting concept for an aluminum desk lamp. They both took it upon themselves to provide valuable design criticism and feedback at several points throughout the process. After countless rounds of refinements, a final design direction was ultimately reached.
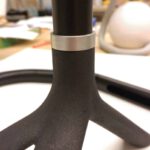
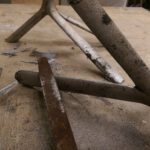
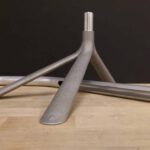
At this time, I was able to speak consult and work with Catalyst’s machining and molding staff. After reviewing the design with Catalyst’s VP of Operations, Ian Papineau, we decided the best way to prototype the lamp was by dividing the concept into two main components. The base would be an aluminum sandcasting that then received multiple machining operations, in order to slide into the bent aluminum tube that constructs the upper portion of the lamp.
With a prototyping plan in place, I approached General Manager, Jason Andrews, about utilizing Catalyst’s CNC machining capabilities to execute all of the necessary secondary operations. With the spirit of collaboration and mentorship in mind, Jason was more than happy to help accommodate my request and made time for me to work with one of Catalyst’s skilled tool makers.
A few weeks and dozens of emails later, I made the trip back to Indianapolis to spend the better part of the a day with Machinist, Bob Leppert, diligently working on the prototype. Bob went above and beyond to ensure that every operation was done with care, craftsmanship, as well as accuracy in mind. Given the tricky task of finding a way to hold down and machine the very organic three-legged base of the lamp, Bob was forced to think outside of the box and the end result was beautiful.
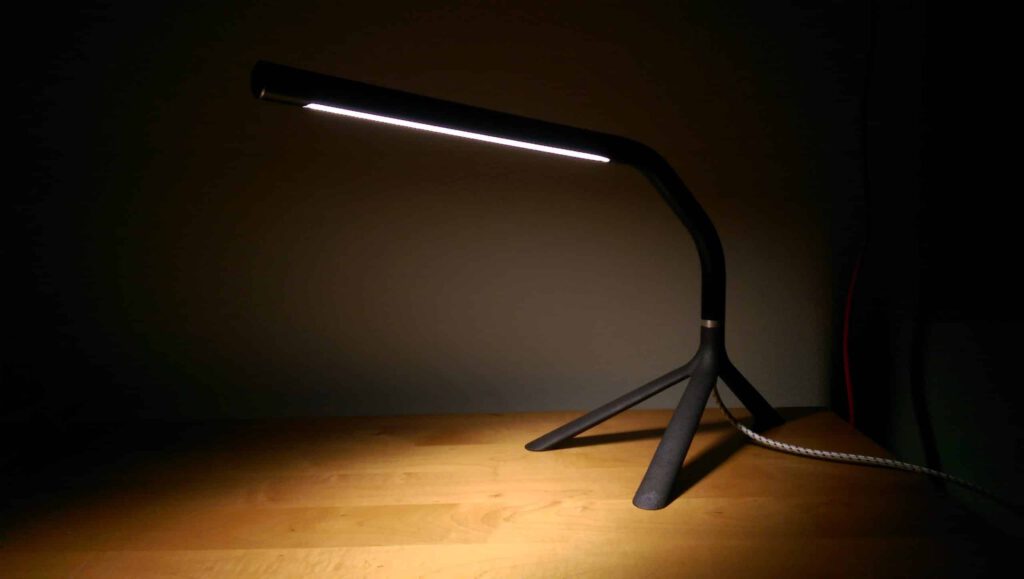
After a trip to have it anodized back in Cincinnati, and a few finishing touches, the lamp was wired up and proudly displayed at the lighting studio’s end of semester exposition in downtown Cincinnati, Switch Lighting and Design. I was exceptionally proud of this piece and all of the labor that went into creating such a seemingly simple thing. This process has been rewarding as both a great educational experience, as well as a lesson in stewardship. With great gratitude to the Catalyst Product Development team, I now find myself with a one of a kind desk lamp, many great memories of collaboration, and an increasingly determined passion for product development.