In recent months, A prototyping technology that has been utilized in the Product Development field for years has become a hot topic. Yes, 3D Printing, or Additive Manufacturing as some may like the more technical term, has come to the forefront as an increased capability not only for manufacturers and Product Development firms, but for individual designer, engineers, inventors and entrepreneurs.
Utilized in almost every market you can think of from automotive and medical devices to toys and juvenile products, 3D printing encompasses many different processes and technologies within its generalized terminology. Fuse Deposition Modeling (FDM), Stereolithography (SL), Selective Laser Sintering (SLS), and PolyJet printing are some, to name a few. All of these processes will produce a visually similar 3D printed model, utilizing different technologies to do so.
Each of these also have their advantages and disadvantages depending on the actual needs and function of the final output required. With so many choices of technologies, processes and materials used in the 3D printing industry, when is it beneficial to your development process, and when should you pursue other methods for creating design models?
Let’s discuss some of the advantages. Again, depending on your output needs/goals at any given time during the product development cycle there could be endless advantages to each of the previous noted 3D printing processes. Here are a few advantages that may simplify your product validation process.
Speed:
- Designers and engineers can turn around actual parts in days or even hours and have the ability to test/validate a design more quickly.
Material Flexibility:
- With so many process options, material flexibility choices are almost endless. Depending on the form, function, and production intent of your design, a material can be selected to mimic the intended material needed for production. Materials with properties from stiffness, flexibility, color and clarity and be chosen. Parts that represent a rubber or TPE specification can even be printed.
- The ability to print two different durometers within one part build can be a huge benefit for a given application.
Design Freedom:
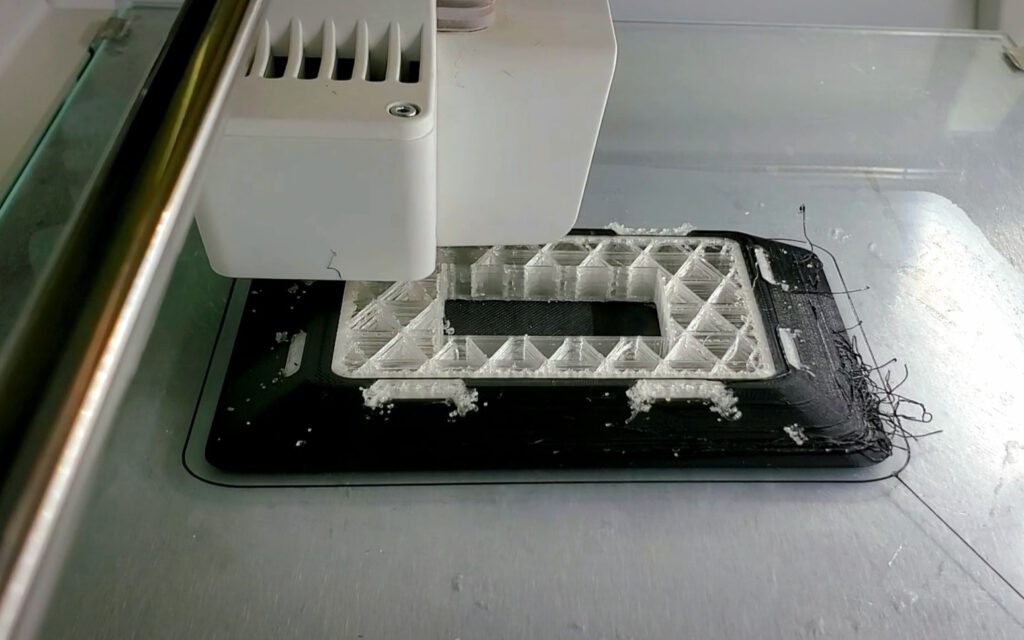
- Though not always recommended, especially if the concept is to continue to a production intent design, the 3D printing process allows for complex designs to be built without manufacturing limitations. This may come in handy for an initial proof of concept model prior to developing detailed engineering and manufacturing intent designs. The process even allows for certain assembly designs to be built as one to reduce the prototype cycle time of having to assemble multiple built components.
- As with almost anything, there is always another side to this story. 3D printing technology, though it has many advantages, also has some disadvantages that may arise as you research or decide upon a 3D printing process to fit your needs.
Costs:
- Equipment and material costs for some 3D printing processes can be a large investment. Depending on your overall intent to utilize the process, the ROI can be longer than expected, especially if you are not directly generating a revenue stream from the output.
- Adding multiple machines that produce different outputs may be of interest if multiple material and part properties are required causing investment costs to rise.
- Additional supporting accessories, such as curing ovens or support structure dissolving tanks, may be required dependent on the process best suited for your prototyping necessities.
Structural Integrity:
- Though 3D printing technologies can give you parts quickly, the output can still have weak or poor mechanical properties as compared to production intent materials. When selecting a process, be sure you are aware of the drawbacks pertaining to the structural integrity of the printed component(s). If structural or fatigue testing is required, it may be beneficial to select alternative methods to produce test components.
Post Process Finishing / Surface Finish Limitations:
- Compared to a component that can be manufactured with a final desired surface finish, texture and color; 3D printed components typically will result in rough surface finishes directly after exiting the build cycle. Additional finishing work, such as sanding, bead blasting, polishing, priming and painting may be required for optimal surface finishes and color results. These additional processes add lead time and costs that will need to be considered.
The trend of 3D printing technologies will continue to grow as equipment and materials reach further development and availability. The technology is likely to grow more into the production / manufacturing realm as these technologies are enhanced for higher volume output. The question on everyone’s mind is when, if ever, will this technology be able to replace traditional manufacturing methods?